株式会社ExtraBold
創業からEXFシリーズ開発のヒストリー

Extrabold(エクストラボールド)は付加製造(3Dプリント)技術を通じて、持続可能性のあるものづくりを分散型の仕組で実現させることをミッションとしています。
量産試作初号機完成までの道のりや、当社の展望についてご紹介します。
創業の経緯
当社の創業は3D技術を活かしたものづくりや人材育成、企業との合同プロジェクトなどを中心に、研究・開発をする株式会社デジタルアルティザンを創業した2017年にさかのぼります。当初から検討していた「マテリアルリサイクルができる大型の3Dプリンターを作りたい」というアイデアをきっかけにスタートしました。
ハードウェア開発には大きな資金も必要となるため、デジタルアルティザンとは別会社にする形で2017年12月に法人化し、3D技術の活用と主に大型3Dプリンタの研究開発を主な事業としています。
創業者の原雄司は大手通信機メーカーで試作現場やCAD設計を経験。その後金型用CAD/CAMメーカーで開発マネージャーを経て、経営者として3Dデータと3Dプリンターに関わるビジネスなど30年以上、デジタルものづくりに携わってまいりました。その過程の中で課題視していたのが大量生産・大量消費・大量廃棄を前提としたビジネスモデルです。環境負荷を軽減し、持続可能性のあるものづくりにシフトすることが、次世代製造業に欠かせないと予見していました。
そのための一つの手段として、リサイクル可能なペレット状の樹脂を材料とした大型3Dプリンターの開発に着手しました。従来のFFF方式(熱融解積層方式)3Dプリンターの課題として、造形品質が工業品グレードの域まで達していないことや、造形に要する時間の長さがあります。このことから3Dプリンターが導入されるシーンは未だ限定的であり、マシニングセンターやレーザー加工機など一般的な工作機械のように普及するまでには至っていません。
一方、製造過程で生まれる樹脂ゴミも製造業においては大きな課題です。日本で1年間に排出される樹脂ゴミのうち、約54%※が企業によるものです。個人が排出する廃プラスチックは洗浄や分別など再利用可能な状態にするまでにいくつもの工程を必要としますが、生産現場で排出するプラスチックは少ないプロセスで再利用が可能です。原は低コストで再利用可能な樹脂ゴミに活路を見出していました。
工業品グレードで早く造形でき、樹脂の廃棄ロスを極限まで削減できる3Dプリンターを製造業に普及させること。これによって大量生産・大量消費からの脱却が加速する。
これこそが当社の描くビジョンでした。
出典元:プラスチック循環利用協会 「2017年 プラスチック製品の生産・廃棄・再資源化・処理処分の状況」
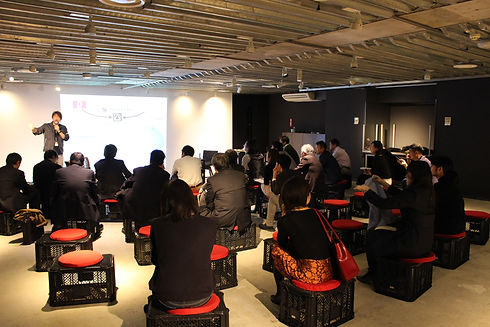
創業当初開催した会社設立説明会の様子
(2017年)
最初の試作機共同開発と体制変更
まず試作機の開発に着手した当社は、既に3Dプリンターを開発・販売をしていた知人のベンチャー企業に大型3Dプリンターの開発企画を持ち込み、共同開発を2018年初頭から開始します。試作零号機「EXF-10」は同年6月に完成し、設計・製造ソリューション展(DMS)に出展し国産初の大型3Dプリンターとして話題になりました。しかし当初の想定よりも早くに試作機の完成にこぎつけたものの課題は多く、製造業の生産現場に導入させるには造形品質の面で抜本的な改善が必要だと考えました。また、共同開発していたベンチャー企業は実験・試作用の3Dプリンターをオーダーメイドで製造するという事業モデルを掲げており、両社のスタンスにギャップがあることも明確になりました。
双方での検討の結果、両社がそれぞれに思い描く3Dプリンターを開発することが3Dプリンターの裾野を広げる上でも最適であるという結論に至りました。こうして2019年に提携を解消し、それぞれが理想とする3Dプリンターを開発することになります。

最初に開発した試作零号機「EXF-10」
造形中の樹脂の反りを抑えるための造形庫内の温度制御の必要性があり、ダンボールのケースを制作。市販のヒーターを使って仮設のチャンバールームを作って運用していた。
量産試作初号機「EXF-12」に至るまで
試作機の設計をゼロから見直すことを決めた当社は設計会社と工作機械メーカー、射出成形品メーカーと開発体制を組み、ゼロベースでの開発をスタートしました。製造業の現場に導入できる品質とスピードで造形できる3Dプリンターを実現するには、工業製品と工作機械を熟知するメーカーの協力が欠かせませんでした。
開発のハードルは非常に高く、実現できないと思われた場面も多々ありました。
しかし、2つの理由から手を止めることはありませんでした。
1つ目は製造業企業からの注目度が高いことです。それまでの活動や商談の中で当社が目指す大型3Dプリンターが市場に受け入れられる可能性は非常に高いことは明確でした。また、国内の製造現場のオペレーター視点に立ったUI・UXを実現した3Dプリンターは市場には無く、その観点でも国産による3Dプリンターの需要は顕在化していました。
2つ目は開発陣の思いです。さまざまなメーカー企業出身の開発者との議論の中で「大型かつリサイクル可能な3Dプリンターがあれば、製造の幅は大きく広がる。CNCなど既にある工作機械のヘッド部分を3Dプリンター用のエクストルーダーに置き換えられるようにしたい」といった共通のヴィジョンがありました。前述したような技術的な課題を解決できれば、製造の現場に3Dプリンターが普及するという確信が当社にはありました。
そして、2020年4月に量産試作初号機「EXF-12」は誕生しました。
量産試作初号機「EXF-12」の組み立ての様子
(2020年2月ころ)


完成した量産試作初号機「EXF-12」
量産機「EXF-12」に至るまで
開発の進捗と併せて、当社の思いに共感する国内企業の支援も増えました。当社が理想とする性能を実現するためには各パーツ、モジュールにおいて高い精度が必要となります。各部品の製造に長けた日本の製造業企業と連携することは、品質の大きな底上げにつながりました。更に2021年4月に資金調達も実施できたことも、開発を前進させる要因となりました。
樹脂を押し出すエクストルーダー部分は新体制の元で実現したものです。安定した出力と大容量かつ高速造形を実現した独自開発のヘッド。今後はさらに様々なCNC工作機械やロボットなどにオプションで装着できるような独自の機構を発案しました。(特許取得)
またFANUC製の制御装置を採用することで、ファームウェアのアップデートによる拡張性は格段に向上しました。他にもメンテナンス性を重視したヒートベッドや庫内温度をコントロールし造形中のソリや変形をできるだけ抑えるためのチャンバールーム、自動消火装置、外部からのリモート操作機能など、製造業のお客様視点で必要と思われる機能を多数実装しました。
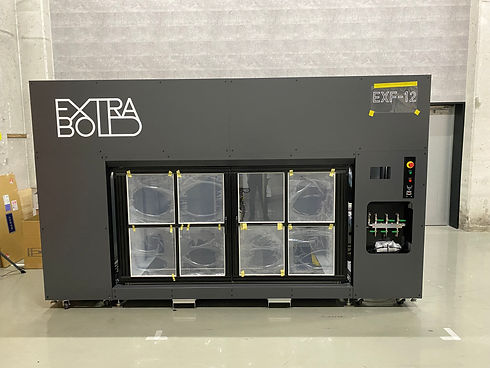
2021年9月にリリースした量産機「EXF-12」
既に導入いただいたお客様からは既存のFFF方式大型3Dプリンターと比較して、圧倒的に造形スピードが早く、安定性も高いことから材料コストを大幅に下げることができたというお言葉を頂いております。
また、自動車向け部品を中心とした鋳造用金型や試作品開発を手掛ける前田技研には、当社のEXF-12の可能性を早期から着目頂きました。ユーザー視点での開発へのアドバイスに加え、EXF-12の導入と併せて当社への出資も決断いただきました。
当社ではシンガポールの大学や研究機関との共同研究を進め、更なる樹脂吐出量の増大や安定的な造形を実現する全く新しい3Dプリントヘッドの先行開発を行っています。また、ソフトウェアにおいては現在も開発を進めており、製品の改善・アップデートと並行して、新たな機能を今後追加する予定です。
更には既存の工作機械に装着できる3Dプリントヘッド(三次元付加製造ヘッド)の研究開発も進めており、製造業現場におけるマテリアルリサイクルを更に加速させます。
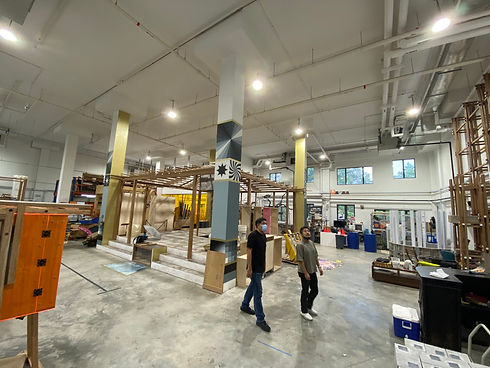
シンガポールの弊社子会社
「ExtraBold R&D Singapore」の拠点
オールメイドインジャパン(All made in Japan)で世界に通用する工作機械を生み出す
EXF-12は工業グレードの製品を製造・加工する工作機械として開発しました。当社は今後も次世代のものづくりを見据えた3Dプリンター及びプリントヘッドの開発に邁進します。
海外ではマテリアルリサイクルや3Dプリンターに代表されるアディティブマニュファクチャリング(付加製造)の研究開発が進む一方で、日本は大きく遅れを取っております。当社はリサイクル可能なマルチマテリアル3Dプリンターを通じて、次世代ものづくりをリードする企業を目指しています。
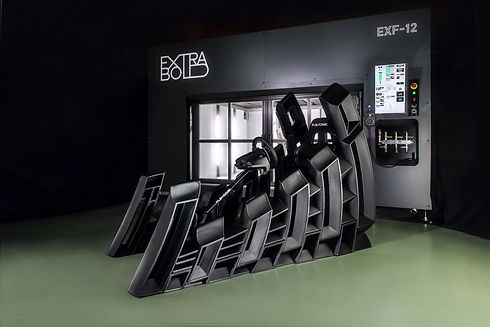
D-WEBERの依頼で前田技研との共同プロジェクトで制作したeスポーツ専用インテリア
「GT EXPERIENCE CONCEPT
若手デジタル人材を育成する仕組
当社では3Dプリンターの研究開発に加え、多種多様なバックグラウンドを活かした人材育成も進めています。デジタルものづくりの研修・共同研究を実施するトレーニングジム「BOLD GYM」についてご紹介します。
当社の活動に関心を持つ企業や大学からのインターンや出向を受け入れ、EXF-12を活用した「デジタルものづくり」の学びと実践の場を提供しています。

